Product classification
CO catalytic combustion equipment
The adsorption of organic waste gas by using the microporous adsorption characteristics of activated carbon is one of the most effective industrial treatment methods. Honeycomb activated carbon has stable performance, The advantages of corrosion resistance and high-speed airflow impact, using its adsorption of organic waste gas can make the purification efficiency as high as 90-95%, activated carbon adsorption saturation can be regenerated by hot air desorption. After regeneration, the activated carbon is put into use again, and the concentration of organic waste gas can be concentrated 10-20 times by controlling the flow rate of the desorption process, The desorption gas stream is heated to about 300 ℃ by the burner device of the catalytic bed, and ignited under the action of the catalyst. The purification efficiency of the catalytic combustion process can reach more than 90%. After combustion, CO2 and H? O are generated and a large amount of heat is released. The heat is used for heating desorption through a part of the heat exchanger in the catalytic combustion bed. The high concentration of waste gas, another part of the heating chamber outside the air used as activated carbon desorption gas, generally achieve desorption ~ catalytic combustion self-balancing process must start the burner for about 1 hour. After reaching thermal balance, the electric heating device can be closed. At this time, the regeneration treatment system relies on the organic solvent in the exhaust gas as fuel, and the regeneration process reaches a self-balancing cycle on the basis of no additional energy, which greatly reduces energy consumption and no secondary pollution. The whole adsorption and catalytic combustion process is automatically controlled by PLC.
Molecular sieve zeolite wheel adsorption concentration device
The molecular sieve adsorption and concentration wheel is a rotary adsorption device prepared by attaching molecular sieve adsorption material to a honeycomb porous carrier. The adsorption material used in the wheel is an inorganic honeycomb hydrophobic zeolite (molecular sieve), so it is usually called a zeolite wheel or a molecular sieve wheel. VOCs molecular sieve wheel adsorption system mainly includes adsorption VOCs molecular sieve core (honeycomb block, HoneycombMonolithicAdsorbent), gas filtration device, rotating device, fan and other components. The adsorption of VOCs molecular sieve core is its core part. The rotating core can be divided into three regions by the partition plate: adsorption zone, regeneration zone and cooling zone. In order to prevent the wind between each area, each area is separated by a partition plate, and the partition plate is made of rubber sealing material with high temperature resistance and corrosion resistance. The rotating core is driven by the motor to run at a certain speed. The molecular sieve adsorption and concentration wheel is divided into adsorption zone, desorption zone and cooling regeneration zone, and the wheel runs continuously at a certain speed. Adsorption zone: after pretreatment of VOCs waste gas by multi-stage filtration device, it enters the molecular sieve wheel adsorption zone for adsorption, and the clean gas after adsorption and purification by zeolite molecular sieve is directly discharged into the atmosphere through the chimney; Desorption zone: Before the adsorption of the molecular sieve in the adsorption zone is saturated, the wheel rotates to the desorption zone, and the high-temperature hot air is used for desorption and concentration. The desorption temperature is 180~220 ℃, and the heat-resistant temperature during operation can reach up to 350 ℃. According to the composition and concentration, the design of a certain rotation speed, can achieve high purification efficiency; in addition, according to the needs of different customer conditions to adjust the adsorption speed and desorption speed, can achieve the ideal VOCs concentration ratio (n =(S1 × V1)/(S2 × V2)= 5~30), the maximum reduction of operation Energy consumption. Cooling regeneration zone: the molecular sieve wheel after desorption enters the cooling regeneration zone, and is cooled and regenerated by cold air or cold exhaust gas. The regenerated molecular sieve wheel rotates to the adsorption zone, continuously adsorbs VOCs exhaust gas, and runs continuously.
Zeolite concentrated rotary RTO
Zeolite concentration wheel device system adsorbs large air volume low concentration volatile organic compounds (VOCs), and then desorbs small air volume high. The concentrated waste gas is introduced into the incinerator to be decomposed and purified; the large air volume and low concentration organic waste gas is passed through a wheel with zeolite as the adsorption material, VOCs is adsorbed by zeolite in the rotary adsorption zone and the purified gas is discharged to the atmosphere through the chimney, and then used in another desorption zone at 180 ℃ ~ VOCs are desorbed by a small amount of hot air at 230 ℃. Such a high concentration and small air volume desorption exhaust gas is then introduced into the incinerator to be decomposed into carbon dioxide and water gas, and the purified gas is discharged to the atmosphere through the chimney. This concentration process greatly reduces the fuel cost. The system is located It is one of the most cost-saving technologies for high air volume and low concentration organic waste gas. The process waste gas removes paint mist dust and particulate pollutants through the pre-filter screen, then adsorbs it through the non-combustible zeolite molecular sieve wheel, and then the clean air is discharged into the atmosphere. As the wheel rotates slowly, it will pass through the desorption zone and desorb it through a small amount of high-temperature desorption air, the high-concentration exhaust gas after desorption is then introduced into a small incinerator or catalytic incinerator to decompose VOCs; the desorption process is equipped with a secondary compensation heater to supply desorption hot air to save energy.
RTO regenerative catalytic oxidation equipment
The organic waste gas is heated to above 760 ℃, so that the volatile organic compounds in the waste gas (VOCs,Volatile Organic Compounds) is oxidized and decomposed into carbon dioxide and water in the combustion chamber. Oxidation of high temperature gas flow through the special ceramic heat storage body, so that the ceramic body temperature and "heat storage", the next process is the exhaust gas from the "heat storage" of the ceramic through the ceramic, the heat transfer to the exhaust gas, organic waste gas through the ceramic as a heat exchanger carrier, repeated heat exchange, so as to save the fuel consumption of exhaust gas heating, reduce operating costs. Under the condition of medium and high concentration, RTO can output waste heat to the outside, and use it in the form of steam, hot air, hot water, etc., to achieve economic benefits while meeting environmental protection goals. The incinerator is mainly composed of ceramic heat storage bed, combustion chamber, burner and electrical control system. The RTO equipment is designed as a three-bed structure, which has the characteristics of high removal efficiency, stable operation and low energy consumption. The exhaust gas containing volatile organic compounds (VOCs) enters the heat storage bed of RTO through the switching of the valve. The exhaust gas is gradually heated by the heat storage ceramic and enters the combustion chamber. VOCs are oxidized at high temperature in the combustion chamber and release heat. When passing through another heat storage bed, the hot air is heat exchanged with the accumulated ceramic to accumulate heat to reduce the consumption of auxiliary fuel. heat storage While the ceramic is heated by hot air, the temperature of the oxidized clean gas gradually decreases, making The outlet temperature is slightly higher than the RTO inlet temperature. Through the switching of pneumatic valves at the bottom of different heat storage beds, the direction of exhaust gas entering the ceramic is changed, and the alternating conversion between the heat storage zone and the heat release zone is realized. When the concentration of VOCs in the system is high enough and the heat energy released is enough, RTO can maintain the oxidation and decomposition conditions of VOCs without fuel, and can output the waste heat of the system to the outside. The heat balance equation is shown in the following figure. RTO equipment in the work, through the following two processes. (1) Cold start preheating state; Fresh air directly enters the RTO main body for preheating. After a certain time T, the inlet and outlet valves automatically switch, and the gas changes its flow direction between beds A, B and C. This process operation evacuates residual organic exhaust gases that may be trapped inside the RTO equipment to avoid hazards during ignition. After 5-10 minutes, the combustion system is turned on by PLC control, the burner system starts to ignite automatically, and the temperature of the regenerative ceramic packed bed gradually rises. After about 3 hours, the top of the ceramic bed reaches about 800 ℃, and the middle reaches about 450 ℃, bottom about 100 ℃. At this point, the preheating process ends. (2) Operation state After the preheating process is completed, RTO enters the operation state. The organic waste gas passes through the ceramic heat storage bed A and is gradually preheated to its spontaneous combustion temperature. Oxidation reaction occurs in the combustion chamber to generate CO and H? O, Then enter the ceramic heat storage bed B to release heat and accumulate heat in the ceramic heat storage bed B. At this time, the C bed is purged, the temperature of the and B heat storage beds gradually decreases from top to bottom, the, B and C beds are switched according to the period T, and the treated flue gas enters the discharge chimney.
Electrostatic tar capturing device
In the production process with coal as raw material, the tar mist particles carried in the semi-water gas are very harmful to the production. First, coal tar can cause blockage of the inlet valve of the nitrogen hydrogen compressor, and oil mist can also cause catalyst poisoning. According to the investigation, if the electric tar catcher is not set in the production process or the coke catching effect of the selected electric tar catcher is not good, the economic loss caused by the valve hole being blocked by the tar and the bounce action of the valve sheet is blocked, and the continuous reduction of the pumping amount is considerable. In coking plants, steel plants, gas plants and carbon plants, the coal tar carried in the gas will damage the operation of the compressor, cause mechanical failure, pollute other equipment in the production process, and reduce the quality of the burning gas. In particular, it will cause the blockage of the gas pipeline, which is very serious. In view of the above situation, the use of safe, efficient and economical electric tar catcher in production is essential to ensure the continuous production of the factory.
Photooxy catalytic waste gas treatment equipment
The use of high-energy UV beam cracking molecular bonds of bacteria in the stench gas, the destruction of bacterial nucleic acid (DNA), and then through the ozone oxidation reaction, completely achieve the purpose of deodorization and killing bacteria.
Low temperature plasma is an interdisciplinary subject based on discharge physics, discharge chemistry and reaction engineering. Low-temperature plasma degradation of pollutants is the use of these high-energy electrons, free radicals and other active particles and pollutants in the exhaust gas, so that the pollutant molecules in a very short time decomposition, and subsequent reactions to achieve the purpose of degradation of pollutants. Widely used in chemical, pharmaceutical, food, leather processing, automobile manufacturing, paint, printing and dyeing, feed processing, garbage disposal and other industries.
Spray tower paint mist treatment equipment for corrosive gases (such as acid, alkaline waste gas) treatment, the current use of liquid absorption method of governance. The key to the treatment of the waste gas by liquid absorption method is the choice of purification equipment. At present, our company has independently developed acid and alkaline waste gas purification processes and equipment with high purification efficiency, simple operation and management, and long service life. The process and products integrate the advantages of similar purification towers at home and abroad, multi-stage rotary spraying and absorption, and at the same time optimize the technical parameters of the packing layer and tower body, with the characteristics of simple structure, low energy consumption, high purification efficiency and wide application range, it can effectively remove water-soluble gases such as hydrogen chloride gas (HCI), hydrogen fluoride gas (HF), ammonia gas (NH3), sulfuric acid mist (H₂ S04), chromic acid mist (CrO3), hydrogen cyanide gas (HCN), alkali vapor (NaOH), hydrogen sulfide gas (H₂ S), formalin (HCHO), etc.
The dust-containing exhaust gas is introduced into the purification tower through the air pipe. When the washing barrel is rotated, the wind belt is accelerated to drive the stuffing ball to fly. In the washing barrel, the dust-containing exhaust gas is fully mixed with water mist for washing and neutralization reaction (when the water is supplemented with acid and alkali). After the exhaust gas is purified, after being dehydrated and defogged by the demisting layer, it is discharged into the atmosphere by a fan or other purification equipment (photo-oxygen catalysis, low-temperature plasma, etc.), the absorption liquid is pressurized by a water pump at the bottom of the tower, sprayed and atomized at the top of the tank, and finally returned to the bottom of the tank for recycling. The purified exhaust gas meets the national emission standard.
Cyclone tower equipment is mainly aimed at viscous dust, oily dust, industrial waste gas pretreatment, fiber dust and other dry dust removal equipment can not handle the working conditions and the development of a new wet and efficient environmental protection waste gas purification equipment, this product is simple and practical, easy to maintain, widely used.
Jingshan Haojie Intelligent Environmental Protection Machinery Technology Development Co., Ltd.
Contact: Mr. Dong+86-13928844138 +86-13774077867
E-mail:1017645596@qq.com
Address: Industrial Plant in the Western Half of Building E2, Intelligent Industrial Park, Jingshan Economic Development Zone, Jingmen City, Hubei Province
Official website:http://en.haojie668.com/
Focus on us
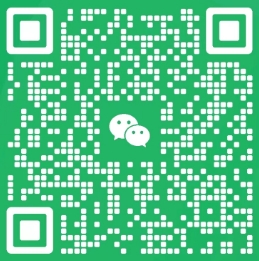
Sweep Code Add
Copyright©2024 Jingshan Haojie Intelligent Environmental Protection Machinery Technology Development Co., Ltd.