





Bag dust collector
Key words:
Biochemical treatment equipment
Flotation equipment
Classification:
Bag dust collector
Chapter I. Overview
Definition and importance of 1.1 bag filter
Bag filter, the standard term "bag filter", is a dry dust removal device that uses a filter bag made of cloth or felt to capture and separate dust particles in the gas. Its working principle is to use the fiber fabric to filter and interception of dust, and separate the dust particles from the airflow through the small pores on the surface and inside of the filter cloth to achieve the purpose of purifying the air. Bag filter plays an important role in the field of industry and environmental protection because of its high dust removal efficiency, wide range of application, stable and reliable operation.
The Role of 1.2 Bag Filter in Modern Industry
With the rapid development of industrialization, the problem of dust pollution in the air has become increasingly prominent, which not only affects human health, but also causes tremendous pressure on the ecological environment. As an effective air pollution control equipment, bag filter is widely used in metallurgy, chemical industry, building materials, electric power and other industries to capture and recover the dust and flue gas generated in the production process of various factories. It helps the factory to reduce the emission of pollutants into the atmosphere, meet the requirements of national environmental protection regulations, and at the same time save resources and improve the recycling rate of materials.
The second chapter, the working principle of bag filter
Filtering function of 2.1 filter cloth
2.1.1 Types and characteristics of filter media
As the core part of bag filter, the material of filter material directly affects the dust removal efficiency and service life. Common filter materials are natural fibers (such as cotton, wool), synthetic fibers (such as polyester, acrylic) and inorganic fibers (such as glass fiber, carbon fiber). Different materials have different physical and chemical properties, such as temperature resistance, corrosion resistance, air permeability and dust removal efficiency. Reasonable selection of filter material is very important to ensure the performance of bag filter.
2.1.2 Microporous structure and dust interception
The filter cloth is usually composed of many small fibers, which form a myriad of microporous structures. When the dust-containing gas passes through, the dust particles larger than the micro-aperture are blocked and deposited on the surface of the filter cloth, thereby achieving effective separation of dust and gas.
2.2 cleaning mechanism
2.2.1 Classification and characteristics of ash removal methods
With the continuous thickening of the dust layer on the surface of the filter cloth, the filtration efficiency increases, and the filtration resistance also increases. Therefore, it is necessary to clean the dust regularly to ensure the continuous and efficient operation of the bag filter. Ash cleaning methods mainly include mechanical vibration, countercurrent blowing, pulse blowing, etc. Each cleaning method has its advantages and disadvantages, such as mechanical vibration structure is simple but may damage the filter bag.
2.2.2 Determination and adjustment of ash cleaning cycle
Determining a reasonable cleaning cycle is essential to maintain the best working condition of the bag filter. The setting of the cleaning cycle needs to consider the gas flow, the nature of the dust, the material of the filter bag and other factors. Through the actual operation test and experience summary, the best cleaning cycle can be obtained and the necessary adjustments can be made.
2.3 dust unloading process
2.3.1 Type and selection of ash unloading device
Dust unloading refers to the process of transferring the dust accumulated in the dust hopper of the dust collector to other containers or transportation equipment. The ash unloading device includes ash unloading valve, ash unloading screw, ash unloading belt, etc. The selection of a suitable ash unloading device requires consideration of the nature of the dust, the amount of ash unloading, the frequency of operation and other factors.
2.3.2 Precautions for ash unloading operation
During the ash unloading operation, attention should be paid to prevent the secondary flying and leakage of dust to avoid secondary pollution to the environment. In addition, attention should be paid to regularly check the sealing and working status of the ash unloading device to ensure the smooth and clean ash unloading process.
The third chapter, the structure of the bag filter
3.1 filter bag and frame
3.1.1 Shape and size of filter bag
The filter bag is a component directly used to filter dust in the bag filter, and its shape is usually cylindrical, flat bag or envelope. The size of the filter bag determines the filter area and the processing capacity of the dust collector, and also affects the cleaning effect and the service life of the filter bag.
3.1.2 The role and material of the framework
The filter bag frame serves to support the filter bag and maintain its shape, and is usually made of metal or plastic. The design of the frame should ensure sufficient strength, while minimizing the friction with the filter bag to avoid damage to the filter bag.
3.2 ash hopper and ash unloading device
3.2.1 Design points of ash hopper
The ash hopper is a container for collecting dust after dust removal from the filter bag. Its design should ensure that the dust can slide down smoothly and avoid dead corners of dust accumulation. The shape of the ash hopper, the angle of inclination and the smoothness of the inner wall are all important factors to be considered in the design.
3.2.2 Selection basis of ash unloading device
According to the nature of the dust (such as viscosity, humidity, particle size distribution) and the use environment (such as temperature, corrosion), the type and material of the ash unloading device are reasonably selected to ensure the smooth ash unloading process and the long-term stable operation of the equipment.
3.3 cleaning and control system
3.3.1 Configuration of the cleaning system
The cleaning system of the bag filter mainly includes the cleaning device, the control instrument and so on. According to actual needs, you can configure timing control, differential pressure control or intelligent control and other control methods to achieve automated management and efficient cleaning.
3.3.2 Function and maintenance of control system
The control system is responsible for monitoring and managing the entire dust removal process, including the control of the dust removal cycle, differential pressure monitoring, and fault diagnosis. Regular inspection and maintenance of the control system is essential to ensure the stable operation of the dust removal system.
The fourth chapter, the application field of bag filter
Application cases in 4.1 industry
4.1.1 Smoke and dust control in iron and steel industry
In the iron and steel industry, ironmaking, steelmaking, steel rolling and other processes will produce a lot of smoke and dust. Because of its high dust removal efficiency, the bag filter is widely used in the smoke and dust control of these processes, which effectively controls the emission of air pollutants.
4.1.2 Fly ash treatment in power industry
Burning coal to generate electricity produces large amounts of fly ash. Bag filter plays an important role in the exhaust gas treatment of power plant boilers. It can not only remove fly ash, but also capture heavy metals and toxic substances to protect the environment and public health. 4.1.3 Dust capture in cement industry
In the process of cement production, the crushing, grinding, calcination of raw materials and the packaging and transportation of finished products will produce dust. The application of bag filter in these links has greatly improved the working environment and reduced the dust content in the atmosphere.
4.2 Commercial and Civil Applications
4.2.1 Indoor air quality control
In indoor environments such as shopping malls, office buildings, and residential buildings, the bag filter can be used as a part of the air conditioning system to remove dust, pollen and other particles in the air to provide a cleaner air environment.
4.2.2 Food Processing and Pharmaceutical Manufacturing
In the food processing and pharmaceutical manufacturing industries, there are extremely high requirements for the cleanliness of the production environment. The bag filter can effectively control the dust pollution in the production workshop and ensure the product quality and safety.
Application 4.3 special environment
4.3.1 Application in High Temperature and High Humidity Environment
In some special industrial production processes, such as drying, sintering and other processes, the dust-containing gas produced often has a high temperature and humidity. The application of bag filter in these environments requires special consideration of the selection of filter materials and protective measures.
4.3.2 Application in Harmful Gas Environment
In the chemical, pharmaceutical and other industries, in addition to dust, but also may be accompanied by the production of harmful gases. Bag filter not only to remove dust, but also need to cooperate with absorbent or catalyst to deal with harmful gases, in order to achieve a more comprehensive environmental effect.
Chapter 5, performance evaluation and optimization
Evaluation method of 5.1 dust removal efficiency
Dust removal efficiency is one of the important indicators to measure the performance of bag filter. By comparing the dust concentration of dust-containing gas before and after entering the dust collector, the dust removal efficiency can be calculated. The evaluation method includes gravimetric method, concentration method, etc., wherein the gravimetric method is calculated by measuring the weight of dust trapped in the filter bag, and the concentration law is determined by measuring the change of dust concentration in the gas.
5.2 Factors Affecting the Performance of Bag Filter
The performance of the bag filter is affected by many factors, including the nature of the filter material, the design of the cleaning system, the flow rate and temperature of the gas, and the characteristics of the dust. In order to maintain the best dust removal efficiency, these factors need to be comprehensively considered and optimized.
5.3 performance optimization strategy
5.3.1 Optimization of filter material and structure
Selecting the filter material suitable for specific working conditions and optimizing the shape and size of the filter bag can improve the dust removal efficiency and reduce the running resistance. In addition, improving the fixing method of the filter bag and reducing the dead zone are also key measures to improve performance.
5.3.2 Optimization of ash cleaning system
According to the dust characteristics and filter bag conditions, adjusting the cleaning cycle and intensity can effectively extend the service life of the filter bag and maintain a low operating resistance. The use of advanced cleaning technology and equipment is also an important aspect to improve the overall performance.
5.4 Future Development Trend and Technological Innovation
5.4.1 Application Prospect of New Materials
With the continuous progress of new material technology, more new filter materials with high performance, corrosion resistance and high temperature resistance may appear in the future, which will greatly improve the application range and working efficiency of bag filter.
5.4.2 Development of Intelligent Control System
The application of intelligent control system can realize the functions of automatic monitoring, fault diagnosis and remote control of bag filter, and improve the convenience of operation and the intelligent level of the system.
5.4.3 Adaptability improvement of environmental protection standards
In the face of increasingly stringent environmental standards and requirements, bag filters need to be continuously improved and upgraded to meet higher standards of emission requirements, including technological innovations in improving dust removal efficiency, reducing energy consumption and reducing secondary pollution.
Chapter 6, Installation and Operation Guide
Preparation before 6.1 installation
Before the installation of the bag filter, detailed planning and preparation are required, including determining the location of the filter, designing a reasonable pipeline layout, and preparing necessary installation tools and materials. At the same time, operators need to be trained to ensure that they are familiar with the equipment structure and operation process.
Key aspects of the 6.2 installation process
During the installation process, special attention should be paid to the correct installation and fixation of the filter bag to avoid damage or fall off due to improper installation. In addition, it is necessary to ensure that all connections are well sealed to prevent air leakage.
6.3 operation steps and daily maintenance
The operation of the bag filter should be carried out in strict accordance with the operation manual, including inspection before starting, monitoring during operation, and maintenance after shutdown. Daily maintenance work includes checking the condition of the filter bag, monitoring the change of pressure difference, and replacing the damaged filter bag in time.
6.4 troubleshooting and emergency treatment
For possible failures, such as filter bag blockage, ash removal failure, equipment leakage, etc., it is necessary to formulate corresponding investigation procedures and emergency treatment measures. Quickly and effectively solve the fault is the key to ensure the normal operation of the bag filter.
Chapter 7, Case Study and Practice Analysis
Case Analysis of 7.1 Industrial Application
By analyzing the application cases of bag filter in different industries, the successful experience and existing problems can be summarized. For example, how to deal with the challenge of high-temperature soot in the steel industry, and how to achieve effective capture of fly ash in the power industry.
Key factors for successful application of 7.2
The successful application of bag filter depends on the correct design and selection, fine manufacturing process, standardized installation and commissioning and strict operation management. These key factors work together to ensure that the bag filter can play its long-term and stable dust removal efficiency.
Related Products
Get a Product Quote
Jingshan Haojie Intelligent Environmental Protection Machinery Technology Development Co., Ltd.
Contact: Mr. Dong+86-13928844138 +86-13774077867
E-mail:1017645596@qq.com
Address: Industrial Plant in the Western Half of Building E2, Intelligent Industrial Park, Jingshan Economic Development Zone, Jingmen City, Hubei Province
Official website:http://en.haojie668.com/
Focus on us
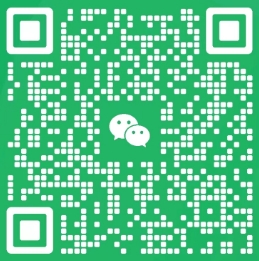
Sweep Code Add
Copyright©2024 Jingshan Haojie Intelligent Environmental Protection Machinery Technology Development Co., Ltd.